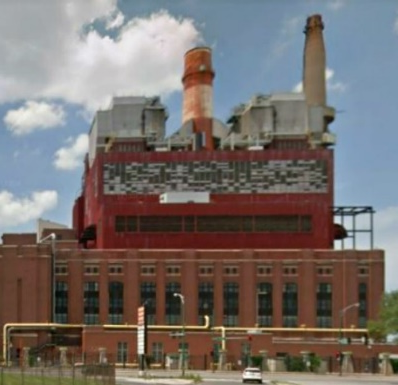
Featured Project
Stapf Energy Services was approached by a coal fired power plant in the Northeast that had been recently mothballed. The plant was sold to a scrap dealer with the intention to sell existing plant equipment.
Following the 2013 Polar Vortex that limited power generation in the region, the existing plant manager believed the plant could operate profitably as a peaking unit given its location within the power grid and a renewed cost structure. Additional fuel sources such as natural gas and biomass would give the plant the flexibility to meet its financial goals.
Stapf Energy Services worked with the Plant Manager and Maintenance Manager, who where the sole employees at the shuttered plant to see if we could support their efforts with the companies we represent. Initial steps included a boiler study to determine how the originally designed coal fired unit would operate firing natural gas. The results of this work along with additional modelling helped develop a conceptual design to initiate the permitting process. Following 4 years of work to support the dynamic process of re-acquiring air permits, the plant successfully restarted as a dual fuel unit burning natural gas and biomass. The plant manager provided the following quote to another plant looking to perform a similar project:
“If this was my project, my very first call would be to Stapf Energy Services. They helped throughout the entire boiler conversion.”
Working with our partners, Stapf Energy Services provided the following support to the project
Dual Fuel Combustion System:
The original firing system (4 corner, tangentially fired) did not perform as expected, with higher emissions and premature burner failures due to flame attachment.
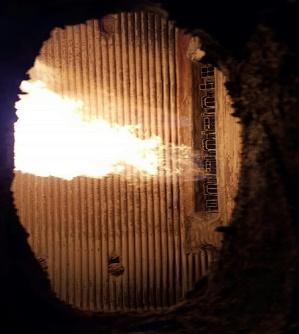
To meet new permits, the combustion system was designed to significantly reduce emissions, particularly at lower loads. New Low NOx Burners, Ignitors, flame scanners, and windbox components were supplied. A proprietary model was run to reconfigure the windbox dampers for optimum control of Over Fire Air, furnace to windbox differential pressure, and improved stoichiometry. Combustion NOx achieved was 25% below the guaranteed value with CO being well under the permitted level.
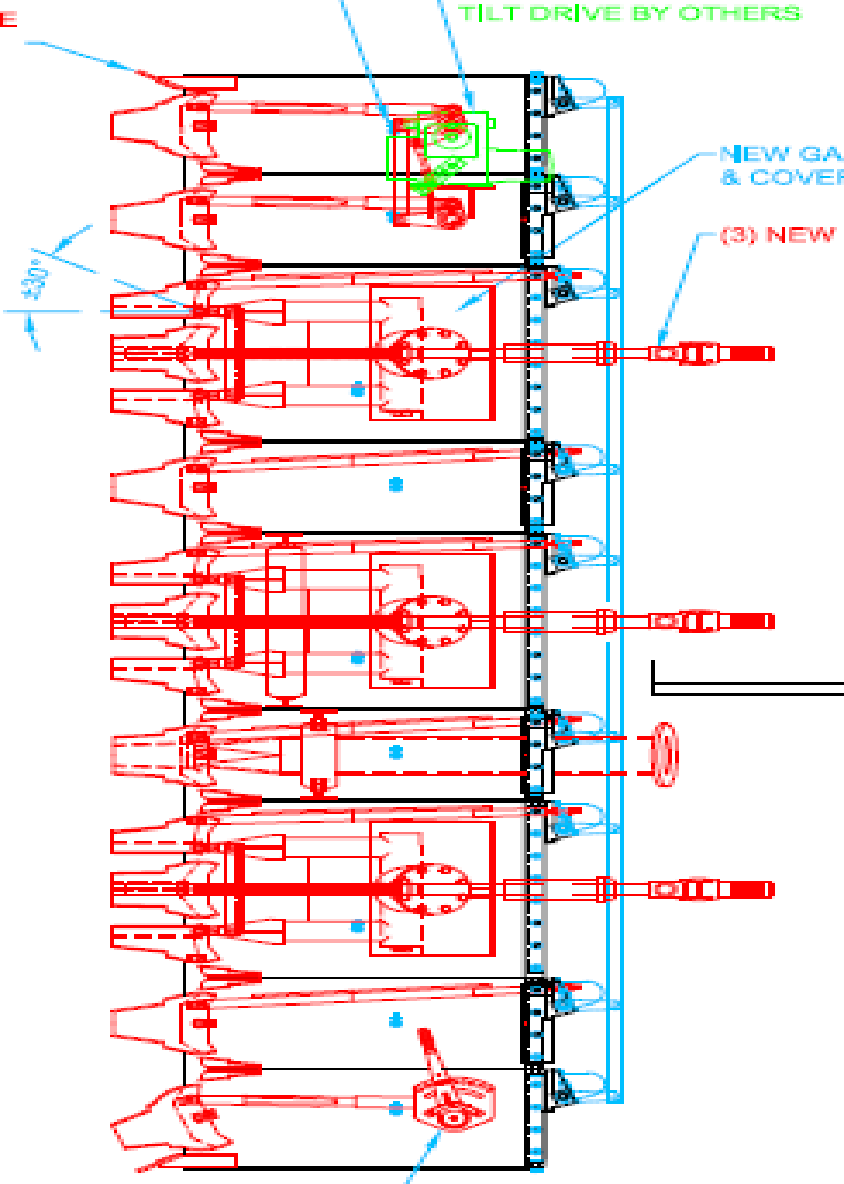
Dual Fuel Combustion System:
The original firing system (4 corner, tangentially fired) did not perform as expected, with higher emissions and premature burner failures due to flame attachment. To meet new permits, the combustion system was designed to significantly reduce emissions, particularly at lower loads. New Low NOx Burners, Ignitors, flame scanners, and windbox components were supplied. A proprietary model was run to reconfigure the windbox dampers for optimum control of Over Fire Air, furnace to windbox differential pressure, and improved stoichiometry. Combustion NOx achieved was 25% below the guaranteed value with CO being well under the permitted level.
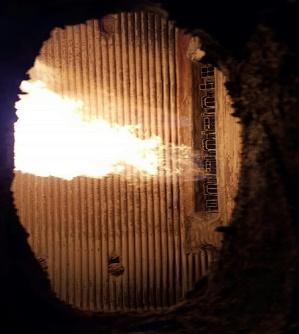
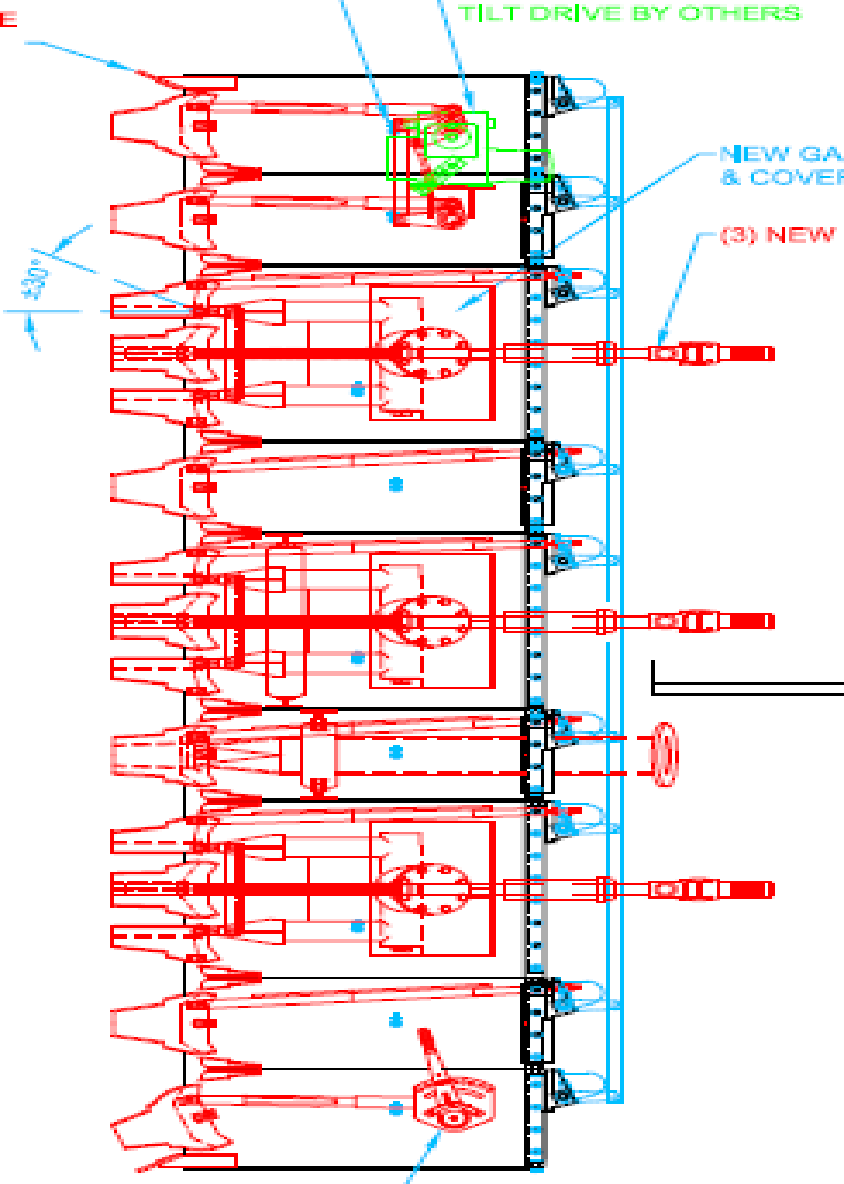
Post Combustion NOx Reduction:
The existing Selective Catalytic Reduction System (SCR) which was designed for coal firing, experienced high velocity and poor distribution. This resulted in lower than expected performance and higher use of reagent. Following CFD modelling, a new static mixer was installed, and the reagent injection points moved to better optimize the SCR with lower ammonia slip, particularly at low loads. A new catalyst was designed and supplied to further maximize NOx reduction. SCR outlet NOx, reagent usage, ammonia slip, and pressure drop where significantly lower than predicted. Operating range of the SCR was lowered to enable reductions at low load.
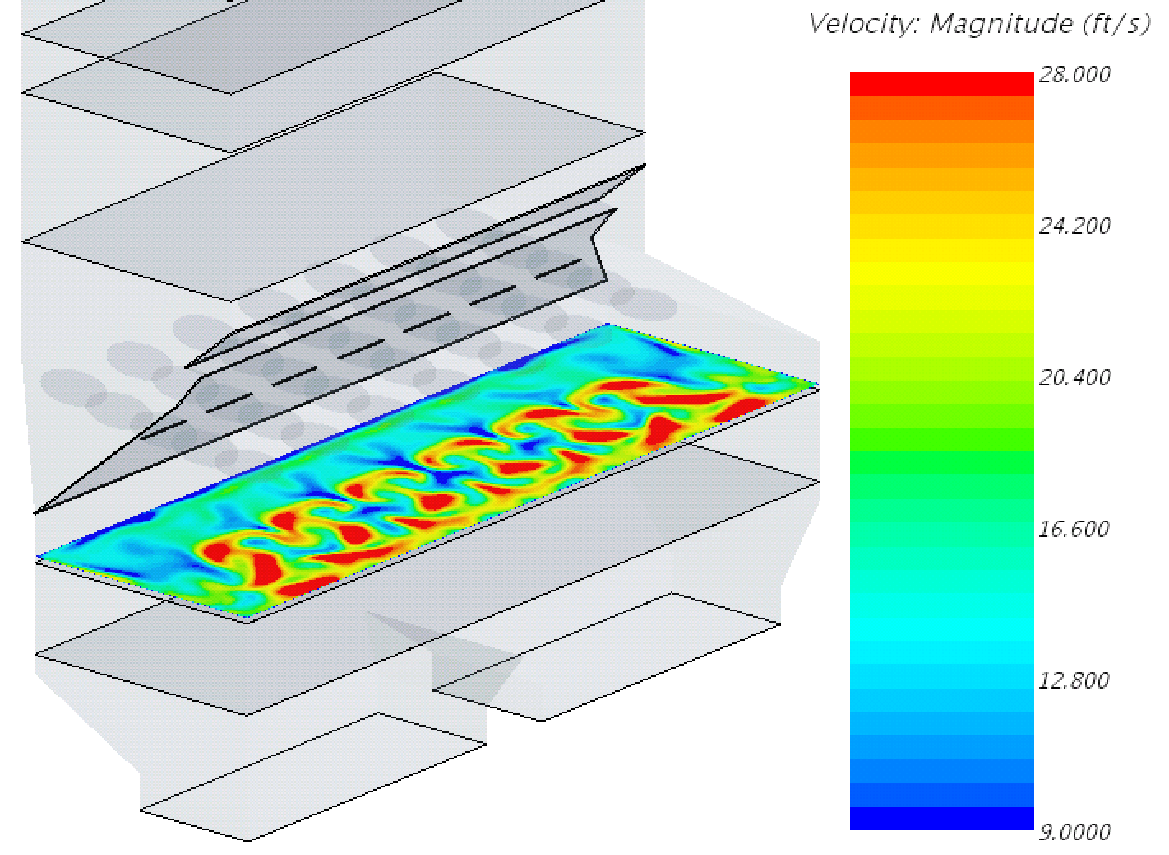
BEFORE
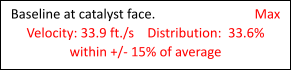
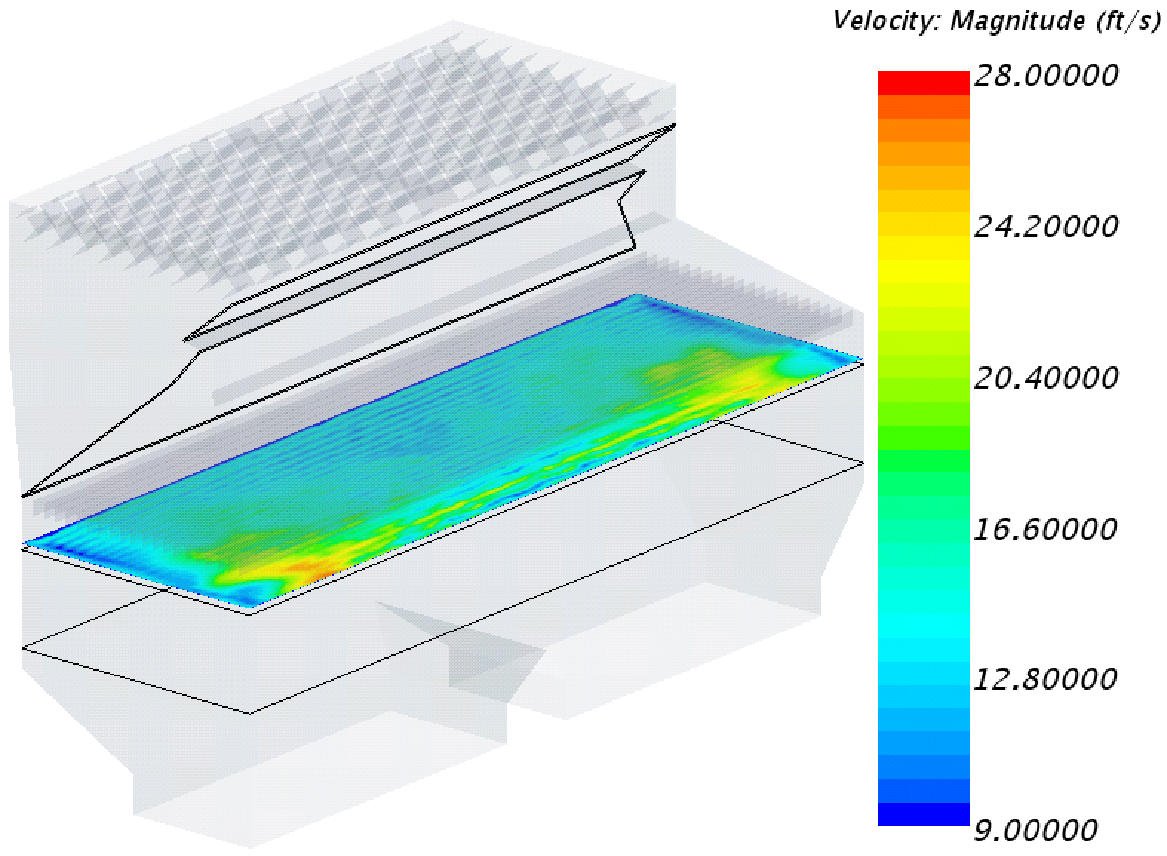
AFTER
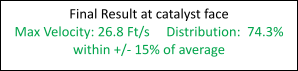
Air Flow Measurement:
FD fan air flow measurement was a Piezometer accurate to only 30%. NFPA requires 30% combustion air. At low load, NOx is important. If instrument error, they could be introducing more air then reading, causing higher NOx. Air Monitor’s VOLU-probe/ Combustion Airflow Management System was installed to accurately measure FD fan air flow. This system is accurate to 2%, ensuring true minimal airflow is being measured. This ensures no additional excess air is being introduced though instrument error which will increase NOx at low load.
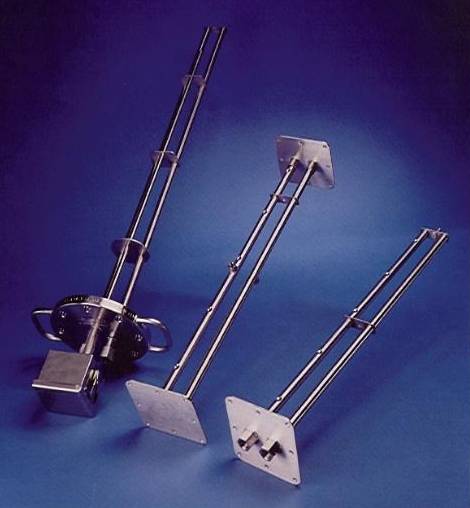
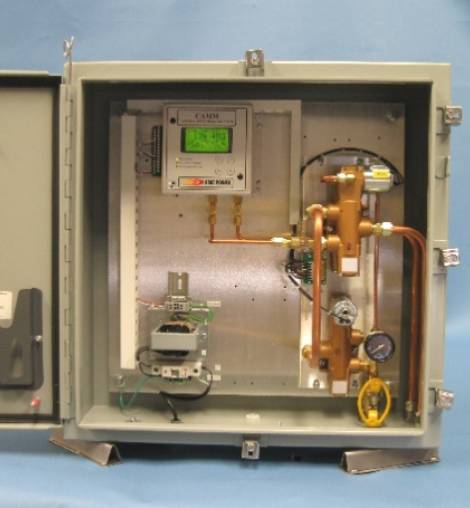
CO Measurement:
The new air permit included stringent NOx and CO requirements across all loads. Low load operation is expected at night and weekends. As the permit did not allow for variances during low load, startup and shutdown, combustion needed to be optimized to its fullest extent. To accomplish this, In-Situ CO monitors where installed at the Economizer outlet. Traditionally, O2 probes have been used to tune combustion. Unfortunately, the O2 measurement captures furnace leakage, so a true reading cannot be determined. The O2 curves are too conservative as they cannot separate combustion O2 from leakage. Delta Measurement has developed a CO measurement system that operates in a dirty flue gas duct such as the economizer outlet. It gives a true measurement of combustion without reading excess leakage and before being mixed by the air heater. Each CO point can be correlated to an individual burner corner which further aids the combustion tuning process on individual burner corners. The graph below shows that 2 corners where producing high CO. After those corners where tuned, CO levels where significantly reduced.
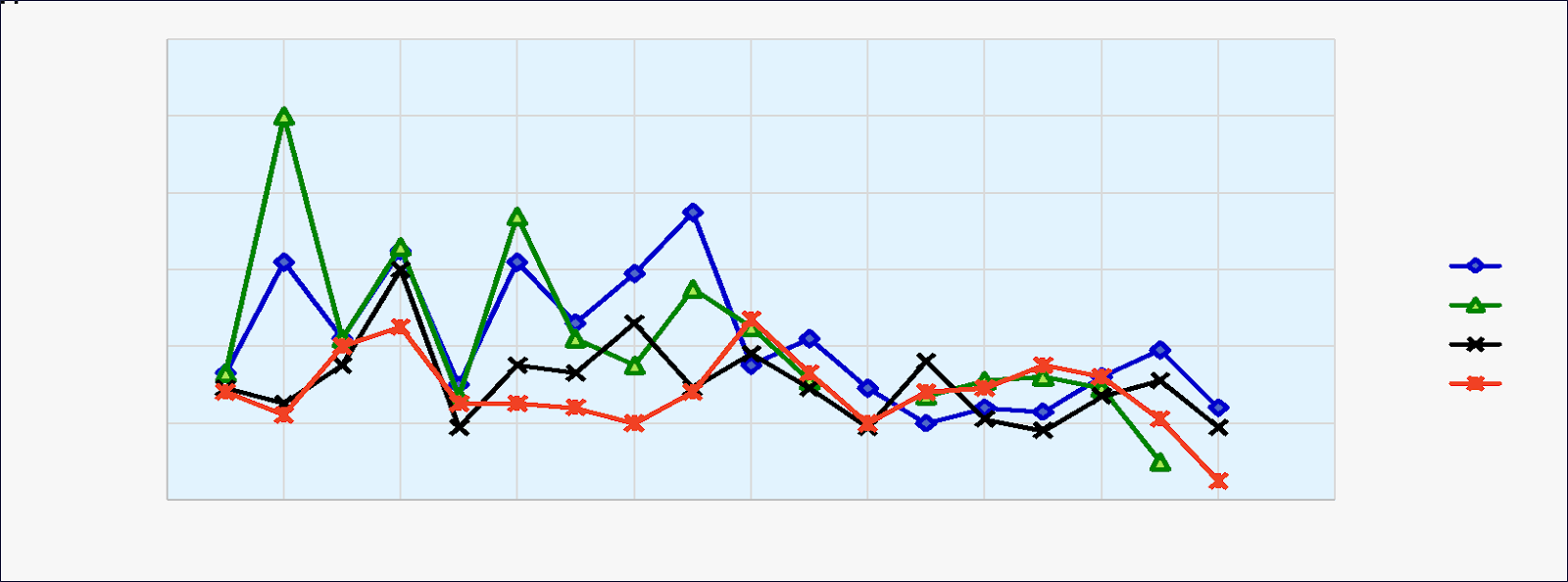
Additional components supplied by our partners included:
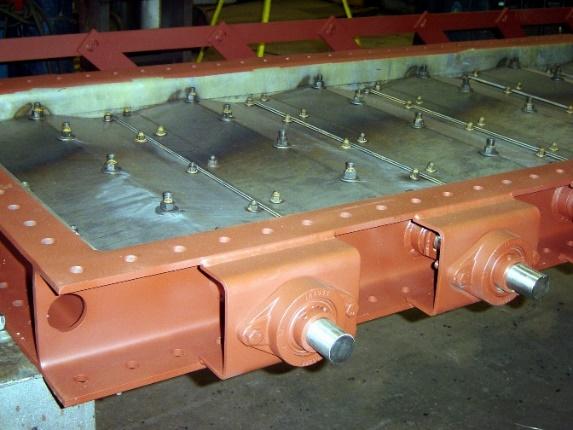
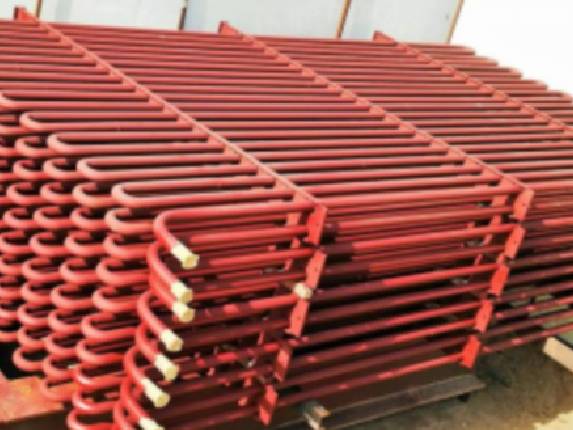
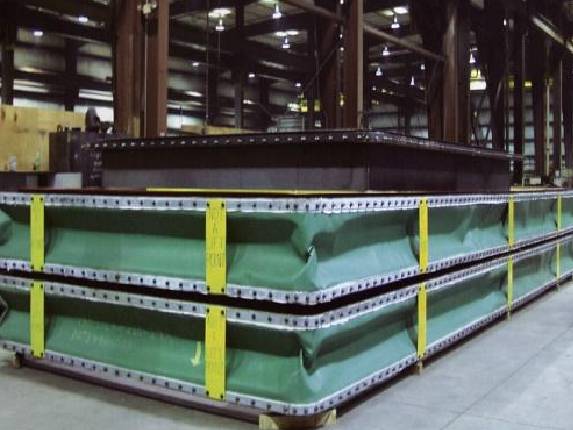
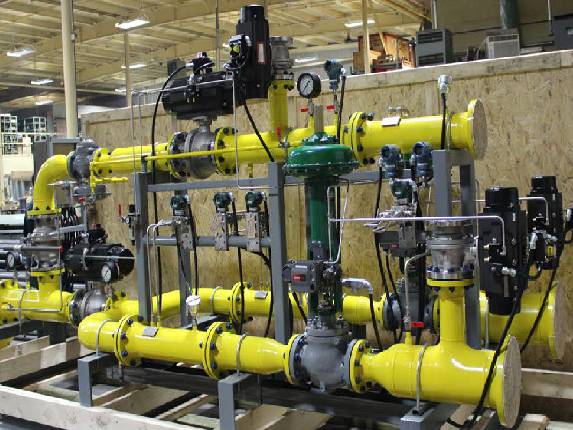
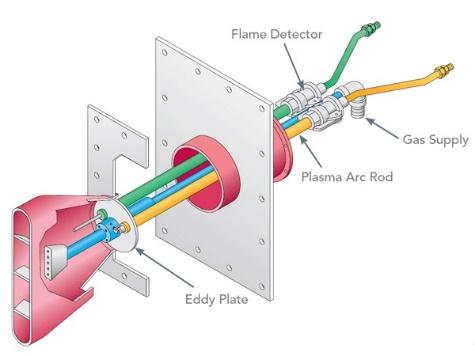
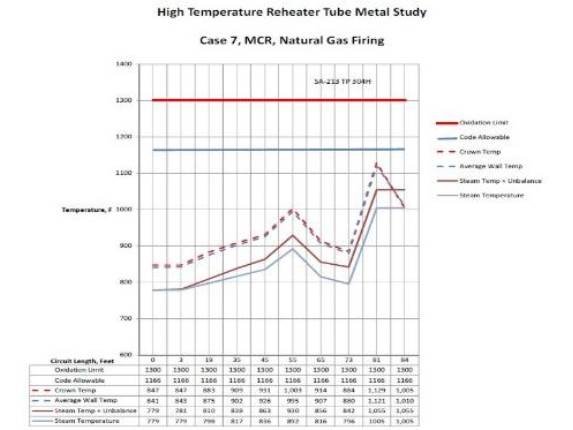
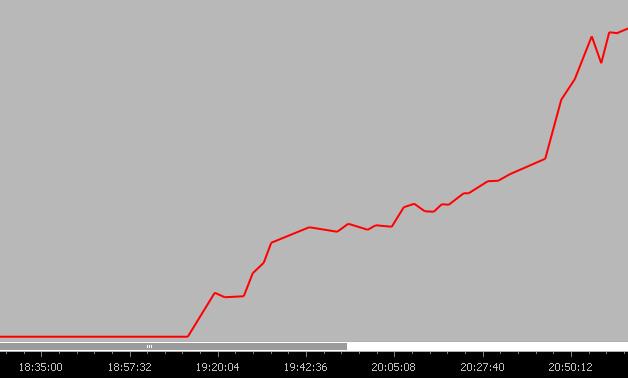